
Process - Clinker and Cement
11 rows · Process includes not specific unit or departmant, includes overall picture of clinker and cement

Cement Clinker - an overview | ScienceDirect Topics
Gypsum is called the retarding agent of cement which is mainly used for regulating the setting time of cement and is an indispensable component. Without gypsum, cement clinker can condense immediately by mixing with water and release heat.

What is Cement Clinker? Composition, Types & Uses - Civil ...
Clinker is a nodular material produced in the kilning stage during the production of cement and is used as the binder in many cement products. The lumps or nodules of clinker are usually of diameter 3-25 mm and dark grey in color. It is produced by heating limestone and clay to the point of liquefaction at about 1400°C-1500°C in the rotary kiln.
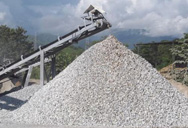
Clinker Production - an overview | ScienceDirect Topics
Cement manufacturing has several opportunities for WHR, specifically in the process step where the clinker material is produced. For clinker production, a mixture of clay, limestone, and sand is heated to temperatures near 1500°C. The kiln and clinker cooler have hot exhaust streams where waste heat could be recovered.

Dry Process Clinker Grinding Bal Mill In Cement Plant
Cement mill.Cement mill is also called cement ball millthe cement mill is key equipment for the grinding process of the cement clinker after the crushing process of it it is mainly used in the cement silicate product industry after long term design and manufacture of the cement mill, our company now has series of cement mill with various specifications to meet with different requirement from.

Cement Kilns Grate Coolers - Clinker and Cement - Clinker ...
the clinker is moved along the grate, and are treated in chronological order of their introduction. Grate coolers exchange heat between clinker and air, and because heat losses are comparatively slight, the thermodynamics of the process is simple Home About this site About cement About clinker List of plants Map of plants Raw materials About Kilns
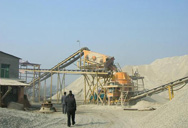
Cement kiln - Wikipedia
A typical process of manufacture consists of three stages: grinding a mixture of limestone and clay or shale to make a fine "rawmix" (see Rawmill);; heating the rawmix to sintering temperature (up to 1450 °C) in a cement kiln;; grinding the resulting clinker to make cement (see Cement mill).; In the second stage, the rawmix is fed into the kiln and gradually heated by contact with the hot ...

Portland cement clinker
Portland cement clinker contains four principal minerals: Alite: approximately tricalcium silicate (typically about 65% of the total) Belite: approximately dicalcium silicate (typically about 15% of the total) Aluminate: very approximately tricalcium aluminate (typically about 7% of the total) ...

Cement Clinker Processing Production Line
A cement plant consumes 3 to 6 GJ of fuel per tonne of clinker produced, depending on the raw materials and the process used. Most cement kilns today use coal and petroleum coke as primary fuels, and to a lesser extent natural gas and fuel oil.

AN INTRODUCTION TO THE CEMENT MANUFACTURING - The …
Cement clinker is grinding in roller mills and ball mills, for example, along with granulated blast furnace slag, fly ash, limestone, and approximately 5% sulfate agents (e.g. gypsum). During production and before leaving the plant, the cement is internally inspected and tested in the plant’s laboratories.

Cement Manufacturing Process | Phases | Flow Chart ...
Aug 30, 2012 · Generally, limestone is 80% and remaining 20% is the clay. Proportioning of raw material at cement plant laboratory. Now cement plant grind the raw mix with the help of heavy wheel type rollers and rotating table. Rotating table rotates continuously under the roller and brought the raw mix in contact with the roller.

Cement clinker grinding plant in Singapore
Cement grinding is the last and the largest power-consuming process in cement production. The process grinds the cement clinker (and gelling agent, performance enhancing materials) into right size with proper gradation. The process also expands the hydrated surface and accelerates hydration, making the cement slurry better meet the cementation ...

How Cement Is Made - Portland Cement Association
The heated air from the coolers is returned to the kilns, a process that saves fuel and increases burning efficiency. After the clinker is cooled, cement plants grind it and mix it with small amounts of gypsum and limestone. Cement is so fine that 1 pound of cement contains 150 billion grains.

Manufacturing of Portland Cement – Process and Materials ...
During this process, these materials partially fuse to form nodular shaped clinker by broking of stone bonds of the raw materials and recombined into new compounds. The clinker is cooled and ground to a fine powder with the addition of about 3 to 5% of gypsum. By …

Wet Process of Cement Manufacturing - Cement Wet Process ...
The wet process of cement manufacturing refers to grinding raw material into slurry after mixing with water and then feeding them into the wet process kiln for drying and calcination and finally forming clinker. The slurry’s water content is usually between 32%-36%.

Cement Production: From Clinker ... - Schenck Process
The clinker is processed into different types of cement. Apart from gypsum and clinker, various additives such as slag sand, trass and fly ash are also ground up with them, depending on the type of cement required. The MULTIDOS® weighfeeder feeds material into …