
Ball Milling | Material Milling, Jet Milling | AVEKA
Ball milling is a size reduction technique that uses media in a rotating cylindrical chamber to mill materials to a fine powder. As the chamber rotates, the media is lifted up on the rising side and then cascades down from near the top of the chamber. With this motion, the particles in between the media and chamber walls are reduced in size by both impact and abrasion. In ball milling, the ...
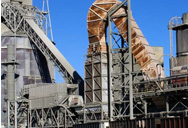
Ball Milling - an overview | ScienceDirect Topics
Ball milling and ultrasonication were used to reduce the particle size and distribution. During ball milling the weight (grams) ratio of balls-to-clay particles was 100:2.5 and the milling operation was run for 24 hours. The effect of different types of balls on particle size reduction and narrowing particle size distribution was studied. The milled particles were dispersed in xylene to ...

Milling Grinding Distribution - Ball Mill
Small Scale Milling Trials To Modify Particle Size. Apr 09 2020 for milling small amounts of a rollercompacted pharmaceutical material gerteis offers a lab tool the small scale mill which reproduces the milling step of the gerteis pactor line it is easy to use and offers the possibility to use different screens with various apertures in order to vary and modify the particle size distribution of

Ball Mill Grinding Particle Size Distribution
Ball Milling Material Milling Jet Milling Aveka. Key properties of grinding media include composition hardness size and density some common types include alumina stainless steel yttria stabilized zirconia and sand ball milling will result in a ball curve particle size distribution with one or …

size distribution of ball mill - techniker-leipzig.de
EFFECT OF BALL SIZE DISTRIBUTION ON MILLING … Ball mills scale up well and in fact improve in performed with increasing size. Ball mills are available in sizes from laboratory scale (also called milling jars) of 0.1 usg to large 5,000 gallon mills. Ball mills are available in various contact materials to accommodate contamination and wear requirements. Chat Here. Effect of ball and feed ...

Ball mill - Wikipedia
Additionally, ball milling has been shown effective for production of amorphous materials. Description. Benchtop ball mill. Laboratory scale ball mill. High-energy ball milling. A ball mill, a type of grinder, is a cylindrical device used in grinding (or mixing) materials like ores, chemicals, ceramic raw materials and paints. Ball mills rotate around a horizontal axis, partially filled with ...
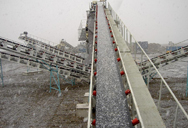
(PDF) EFFECT OF BALL SIZE DISTRIBUTION ON …
PDF | On Sep 23, 2009, François Mulenga Katubilwa published EFFECT OF BALL SIZE DISTRIBUTION ON MILLING PARAMETERS | Find, read and cite all the research you need on ResearchGate

EFFECT OF BALL SIZE DISTRIBUTION ON MILLING PARAMETERS
2.6.1 Ball size distribution in tumbling mills 37 2.6.2 Milling performance of a ball size distribution 40 2.7 Summary 41 Chapter 3 Experimental equipment and programme 43 3.1 Laboratory grinding mill configuration 43 3.2 Preparation of mono-size grinding media 44 3.3 Feed material preparation 46 3.3.1 Coal sample collection at Tutuka power station 46 3.3.2 Feed preparation for laboratory ...

Effect of ball and feed particle size distribution on …
In this article, alternative forms of optimizing the milling efficiency of a laboratory scale ball mill by varying the grinding media size distribution and the feed material particle size distribution were investigated. Silica ore was used as the test material. The experimental parameters that were kept constant in this investigation was the grinding media filling, powder filling and the mill ...

Lab Report 1 and 2: PRACTICAL 1 : BALL MILLING
PRACTICAL 1 : BALL MILLING AIMS: 1. To grind the given material to a smaller size using a ball mill 2. To obtain the size distribution of the initial and the final mixture by sieving. 3. To analyze the results using the available theories. INTRODUCTION: Ball Mill is the equipment to be used for size reduction. It is a kind of grinder used for intermediate or fine grinding. Ball mill is a metal ...

Ball Milling Ball Mill Particle Sie Distribution
Ball Milling Ball Mill Particle Sie Distribution. In this article alternative forms of optimiing the milling efficiency of a laboratory scale ball mill by varying the grinding media sie distribution and the feed material particle sie distribution were investigated. Silica …

Ball Milling Ball Mill Grinding Particle Sie …
Ball Milling Ball Mill Grinding Particle Sie Distribution. 2020-5-30The particle sie distribution was observed after 20 40 60 80 100 150 200 and 300 ball mill revolutions. The energy input was calculated from the net torque corrected for the torque for the empty mill and the number of revolutions . Get Price List Chat Online. Product New. Our products sell well all over the world. Production ...

Ball Mill: Operating principles, components, Uses ...
A ball mill also known as pebble mill or tumbling mill is a milling machine that consists of a hallow cylinder containing balls; mounted on a metallic frame such that it can be rotated along its longitudinal axis. The balls which could be of different diameter occupy 30 – 50 % of the mill volume and its size depends on the feed and mill size. The large balls tend to break down the coarse ...

Sie Distribution Between A And Ball Mill
Ball Milling Material Milling Jet Milling Aveka. Ball milling is a size reduction technique that uses media in a rotating cylindrical chamber to mill materials to a fine powder as the chamber rotates the media is lifted up on the rising side and then cascades down from near the top of the chamber. Oline Chat; Ball Size Distribution For The ...

Effects of Ball Milling Processing Conditions and …
15.04.2019 · The effects of processing parameters in ball milling and the different behaviors of Cu-Nb and Cu-Mo alloys during milling were investigated. High powder yields can be obtained by changing the BPR value and ball size distribution and no clear dependence of BPR value on powder yield can be found from the experiment results. The addition of oxygen ...

Charge Media Distribution Inside Ball Mill
Charge Media Distribution Inside Ball Mill. We are a large-scale manufacturer specializing in producing various mining machines including different types of sand and gravel equipment, milling equipment, mineral processing equipment and building materials equipment. And they are mainly used to crush coarse minerals like gold and copper ore, metals like steel and iron, glass, coal, asphalt ...

Milling - Our Equipment - British Rema
This single unit is capable of milling materials up to a hardness of 10 Mohs and enables accurate and highly controllable particle sizes to be achieved, typically with narrow size distribution. A range of mill sizes is available for throughputs ranging typically from 0.5kg to 2 tonne per hour with average particle sizes as low as 1 to 2 microns.

ball mill charge machine size distribution
Comparison of particle size distribution after 3D ball milling with that after 2D ball milling Ordinate Volume Abscissas Particle diameter For 2D refinement occurs some extent with increasing primary peak height and decreasing secondary peak height accompanying peak shift to … Chat Online. Mono Chamber Ball Mill Page 1 of 2. Re Mono Chamber Ball Mill Hi Fjalali Thanks for sharing the more ...

determining the particle size distribution from a …
Planetary Ball Milling . Particle Size Distribution Effects that Should be Considered - This valuable mineral particle size distribution is not characterised by the solids P80 of thumb that laboratory rod milling rather than ball milling produces a size distribution most and investigated to determine if it matches that expected (or.