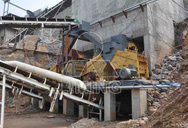
Effects Of Impurities In Iron Ore Pellet Plant
pelletization process wastes . Iron Ore Processing for the Blast Furnace. The following describes operations at the National Steel Pellet Company, an iron Creating steel from low grade iron ore requires a long process of mining, crushing, (with the most impurities removed) becomes the final concentrate.

effects of impurities in iron ore milling plant
effects of impurities in iron ore milling plant Froth Flotation of Iron Ores - sapub Our calcium- and magnesium-based products and minerals are used throughout the iron- and steel-making process as binders or flux agents to form slag. Slag removes harmful impurities, such as silica, phosphorus and sulfur.
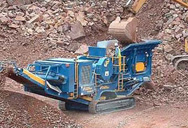
(PDF) Effect of Impurities on Steelmaking
A range of impurities in lump, fines and pellet products will be discussed based on the operation of sinter plant, blast furnace and steel making processes. These impurities impact on the steel...

effects of impurities in iron ore pellet plant
effects of impurities in iron ore pellet plant Iron and Types of Iron | ispatgu Pure iron is silvery white colored metal and is extremely lustrous Its most important property is that it is very soft [Chat Online]

effects of impurities in iron ore pellet plant , CIS
Effects Of Impurities In Iron Ore Pellet Plant. effects of impurities in iron ore pellet plant. This is when solid particles stick to one another, and while this is an undesirable feature in many powder and particle processing operations, it is essential for the successful sintering of iron ore

Variables Affecting Iron Pellet Properties
Data on the influence of alumina and silica are therefore primarily of interest for assessing the likely effects of uncontrollable changes in the gangue content of iron ore used as pellet plant feed. Lime and Blaine index are variables which can be controlled at the feed preparation stage of a pellet plant.

(PDF) Iron Ore Pelletizing Process: An Overview
The use of binders for iron ore pelletizing is required to: (a) increase the pellet strength before heating – green strength; (b) prevent the collapse of the pellets during firing, when the ...

ALTERNATIVE BINDERS TO BENTONITE FOR IRON ORE …
iron ore, water and a binder are balled in a mechanical disc or drum to produce wet pellets. Bentonite is the most widely used binder in iron ore pelletizing industry. The use of bentonite is favorable in terms of physical, mechanical and metallurgical pellet properties, however, because of its acid constituents (SiO 2 …

Beneficiation Plants and Pelletizing Plants for Utilizing ...
such as sulfur and phosphorus. The iron ore and major impurities have a similar hydrophilicity; but adding a stone (collector agent) that is adsorbed selectively to either iron ore or impurities makes the surface with the adsorbed agent hydrophobic. Air bubbles are then charged from the bottom to be

Iron Ore Testing Laboratory | Mineral Testing Labs | Mitra ...
Modern steel mills and direct-reduction iron plants transfer the molten iron to a ladle for immediate use in the steel making furnaces or cast it into pigs on a pig-casting machine for reuse or resale. Modern pig casting machines produce stick pigs, which break into smaller 4–10 kg pieces at discharge. Effects of Iron Ore Elements on Steel Making

Introduction to Iron ore Pellets and Pelletizing processes ...
Formation of oxides and slag bonds is decisive of this stage. Bonding of mineral grains developed during induration of pellets is affected by the three factors consisting of (i) solid oxide bonding, (ii) re-crystallization of iron oxide, and (iii) slag bonding.

The Effect of Lime Addition on Reduction of Iron Ore Pellets
Effect of Lime Addition upon the Behavior during Reduction of the Pellets. Attempt to Interpret the Causes of Swelling, Loss in Strength and stone Disintegration. For the commercial production of iron ore pellets from hematite ores, as it is practiced in various pellet plants, the addition of lime has shown to be an efficient means with a view to improving cold compression and abrasive strength of the …

Iron Ore Pellets: North America, BF and DR Grade, Supply ...
Iron Ore Pellets: North America, BF and DR Grade, Supply and Quality ... Planned DR Pellet Plant Projects to Serve NAFTA. BF Pellet Quality . DESIRED BLAST FURNACE PELLET CHARACTERISTICS • High iron content • minimal impurities • high level of cold strength; tumbler > 95 % abrasion < 5% • narrow size range, > 80 % 9.5 x 12.5 mm ...

Iron Ore - an overview | ScienceDirect Topics
At temperatures of approximately 1500°C, silicate and aluminate impurities from the ore and fuel combine with the flux to form a molten slag. This slag, being less dense than the molten iron, floats and can be tapped off.

Iron Ore Pellet - an overview | ScienceDirect Topics
In this route of iron making, the use of noncoking coal or natural gas is made as reductant for iron ore. The oil is used for heat hardening of iron ore pellets which is generally exploited by gas-based DRI plants. The coal-based DRI units generally require lump ore which need some electrical energy during crushing and sizing operations.

Effectiveness of Organic Binders for Iron Ore Pelletization
availability of cheaper and superior iron ore pellets from foreign sources and to the decline in domestic steel consumption. The decreased demand had a dramatic influence on the iron ore industry, as shown by the production stoppage (closing) of two of eight pelletizing plants …

Iron ore - Wikipedia
Lower-grade sources of iron ore generally require beneficiation, using techniques like crushing, milling, gravity or heavy media separation, screening, and silica froth flotation to improve the concentration of the ore and remove impurities. The results, high-quality fine ore powders, are known as fines. Magnetite. Magnetite is magnetic, and hence easily separated from the gangue minerals and ...

iron ore pelletizing plant
Vales Pelletizing Plant in Oman. Pelletizing is a process that involves mixing very finely ground particles of iron ore fines of size less than 200 mesh with additives like bentonite and then shaping them into oval/spherical lumps of 8-16 mm in diameter by a pelletizer and hardening the balls by firing with a fuel.

Production Plant Of Iron Ore In Pune India
The Indian Iron Ore Pellet Industry - A Report JPC 9 Total production in the Indian iron ore pellet industry stood at 27.64 million tonnes during the reference year 2013-14. After accounting for own consumption of 16.08 million tonnes, production for sale stood at 10.04 million tonnes in 2013-14.