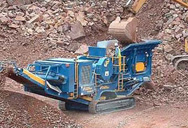
Bilder von in feed grinding process
In-feed grinding — also called plunge grinding — is used to grind cylindrical parts with notches or complex shapes, such as gear shafts. Here, the workpiece rest blade needs to be tooled to match the shape of the part. The grinding and regulating wheels must be dressed to match the part’s desired profile cut.
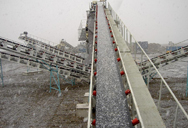
What is Creep Feed Grinding and how does it …
Creep feed grinding is characterized by lower workpiece speeds and higher depths of cut resulting in a larger arc length of contact between the grinding wheel and workpiece when compared with reciprocating or pendulum grinding. Creep feed grinding achieves significantly higher productivity in mass production compared to reciprocating grinding. With todays conventional, highly porous …
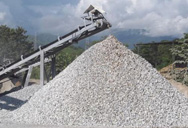
Infeed Grinding | TGS Centerless Grinders
Infeed Grinding. Infeed centerless grinding is used to grind parts that require multiple diameters and profiles to be ground at one time. The part is loaded onto the blade and pushed against a stop to hold it stationary. With the necessary form dressed into the grinding wheel and the regulating wheel, the grinding wheel is fed into a specified depth.

Plunge Grinding or In-feed Centerless Grinding - …
Unlike the through-feed grinding process which pulls the workpiece past the grinding wheels, the workpiece in in-feed is held and supported between the wheels for a thorough grinding even in the smallest part diameters. The different processes involved in the centerless grinding operation all happen in a single pass with an automated course. Grinding machines have the ability to grind …

TYPES OF GRINDING PROCESS - Mechanical …
In-feed grinding is different from through-feed grinding process. If we have a workpiece, which has not exactly not right circular cylindrical shape, in this situation we will prefer in-feed grinding process as grinding wheel could be dressed according to the workpiece surface. Grinding wheel will be feed in radial direction in case of in-feed grinding process. In-feed grinding consumes lots of time in …

in feed grinding process
in feed grinding process. Van Aarsen is also looking to increase the nutritional value of feed through its splitgrinding technological innovation said van Kempen Splitgrinding she said involves the separation of one batch of raw materials into two subbatches that are individually dosed and ground. Whatever your requirements, you ll find the perfect service-oriented solution to match your ...
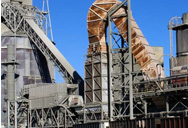
Differences Between Thru-Feed And In-Feed …
In-feed grinding is also a form of centerless grinding. This process, however, is optimized for workpieces with complex or abnormal shapes. The workpieces must be manually loaded into the grinding machine and then the regulator wheel is manually moved, as well. This process is optimal for complicated parts and wheel shapes.

Chapter 18. Feed Milling Processes - stone and …
Grinding also increases the total surface area of a given weight of feed, thereby allowing more space for steam condensation during the conditioning process. This results in a higher feed temperature and more water absorption which together, within the time available, increases gelatinization of raw starch. Starch gelatinization has been mentioned previously (Section 3), but since it is the key to water …
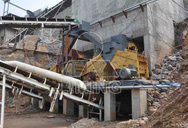
In-feed Grinding - Centerless grinding, tight …
In-Feed centerless grinding is available for parts that have shoulders or obstructions not allowing them to pass in between both the regulating and grinding wheels. We have the capability to hold tight tolerances and ensure critical features are met per customer specification.

Basics of Grinding - Manufacturing
The application of coolants to the grinding process is important. Coolants reduce grinding machine power requirements, maintain work quality, stabilize part dimensions, and insure longer wheel life. Coolants are either emulsions, synthetic lubricants or special grinding oils. Coolants are applied by either flooding the work area or by high pressure jet streams. Types of Grinding There are many ...

Frequent problems during grinding – grindaix …
So that a grinding process runs without the occurrence of grinding burn, it is essential to ensure an adequate coolant lubricant supplyto the machining zone. A large proportion of the waste process heat is bound and transported away in the coolant lubricant. Only part of the heat generated is taken up by the part, thereby lowering the risk of grinding burn considerably. Frequently, coolant ...

Grinding Process - Mineral Processing & Metallurgy
The present chapter will be devoted to a study of the process of grinding within a real mill. Since within a “tumbling” type of mill the size reduction can result from direct crushing, from shearing or abrasion between the particles in the feed, between the particles in the feed and the mill bodies or between the particles and the mill lining, the process is much more complicated than in ...
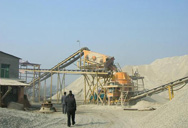
Centerless Thrufeed, & Infeed Grinding Services
Infeed also known as In-feed is a centerless grinding process, where complex shapes are being formed on a workpiece such as an hourglass shape. Infeed grinding requires more preparation by accurately setting the regulating wheel into place. Once the Infeed centerless grinding wheel has been "dressed" for the workpiece, the process begins. Infeed centerless grinding is best suited for ...

Centerless grinding - Wikipedia
End-feed grinding is best for tapered workpieces. In-feed. In-feed centerless grinding is used to grind workpieces with relatively complex shapes, such as an hourglass shape. Before the process begins, the workpiece is loaded manually into the grinding machine and the regulating wheel is moved into place. The complexity of the part shapes and grinding wheel shapes required to grind …

in feed grinding process - MC Machinery
Through feed grinding process is considered as quite productive as grinding process . Special Grinding Processes - Creep Feed Grinding / Dr. 2006-04-15 Generally, the creep-feed grinding process is marked by a special mode of operation. As illustrated in Fig. 3, in contrast to the conventional grinding technique, the depth of cut per pass or revolution is increased 1000-10,000 times and the ...

What is Thru Feed Grinding? | Lapmaster Wolters
Thru-Feed Grinding is a production flat machining process that does almost everything a conventional double disc or vertical spindle grinder can do. Thru-feed grinding is the most efficient method known for high production surface grinding of small to mid size parts because it practically eliminates non-productive time. With the Thru-Feed Grinder, all machine time is grinding time, little is ...

Grinding burn - Preventing and Monitoring! – …
The term grinding burn while grinding is understood as the thermal damage of a ground part caused by an incorrect grinding process. Grinding burn is caused by excessive heat dissipation into the part material. As materials cool as rapidly as they heat, the material undergoes a treatment similar to a tempering process. At high enough tensile stresses, caused by the grinding burn at the outer ...

8 Principles of Centerless Grinding - Metal Cutting ...
In-feed grinding — also called plunge grinding — is used to grind cylindrical parts with notches or complex shapes, such as gear shafts. Here, the workpiece rest blade needs to be tooled to match the shape of the part. The grinding and regulating wheels must be dressed to match the part’s desired profile cut. The regulating wheel spins the part at one speed while pushing it towards the ...

1. Grinding 1.1. Grinding and Abrasive Machines
grinding, such as wheel speed, coolant flow, maximum and minimum feed rates, and grinding depth. stone size determines the physical abrasive size in the wheel. A larger stone will cut freely, allowing fast cutting but poor surface finish. Ultra-fine stone sizes are for precision finish work, where a fine surface finish is required. The wheel bonding agent determines how the wheel holds the ...